Carbon Fibre | Applications in Aerospace
- Evie Wilson
- Dec 2, 2022
- 4 min read
Updated: Aug 4, 2023
Touted as the ‘material of the future’, carbon fibre is a highly popular invention leading the way in the fields of aerospace, civil engineering, motocross, and the military. If you need a strong and lightweight material, carbon fibre is the crème de la crème, and is sure to pave the way for technological advancements in the future.

When was carbon fibre discovered?
Carbon fibre was discovered in 1860 by Sir Joseph Wilson Swan and was originally used in an incandescent light bulb. It wasn’t until the last half of the 20th century that manufacturing processing improvements were able to create the carbon fibre that is commercially used today, distinct in its strength-to-weight and stiffness-to-weight ratios.
How is Carbon Fibre made?
A complicated, multistep manufacturing process is required to manufacture carbon fibre. To this day, the process of producing aerospace-grade carbon fibre requires expensive facilities and equipment with a tiny margin of error.
CARBONISATION
The first step in the process of making carbon fibre is called carbonisation. This involves taking thin plastic filaments called PAN (polyacrylonitrile) and chemically altering them to produce a perfect chain of carbon atoms.
The filaments are lined up and sent through an oxidation oven (around 400℉) which helps the fibres to pick up oxygen atoms, rearranging the atomic structure of the threads. This helps them to become more heat resistant. By the end of the process, the almost white threads turn black.
The fibres are heated in an oxygen-free gas mixture in a furnace which bonds the carbon atoms into a tight crystal structure. The fibres are later sent through electrified water which etches the surfaces of the threads, allowing them to absorb resin more easily.
SURFACE TREATMENT
After carbonising, the surface is then treated by being slightly oxidised, making the surface rougher and enhancing its mechanical bonding properties.
SIZING
Lastly, the carbon fibre undergoes ‘sizing’ - covering the material in a resin. Once the threads are locked together following the above processes, they are then rolled onto a spool to be used as carbon fibre fabric, or moulded into a product. The latter is referred to as prepreg, which needs to be cured in an oven to ensure maximum durability.
Et voila! Carbon fibre is made.
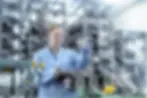
Qualities of carbon fibre
Stronger than steel yet far lighter. Five times stronger than steel in fact.
High stiffness
High tensile strength
Low weight
High chemical resistance
Low thermal expansion - it doesn’t change its shape, area, volume, or density in response to a change in temperature
Repeatable - can use it for moulds to allow for high versatility
Radiolucent - invisible in X-rays and transparent to radiation
Drawbacks
Carbon composites can break or shatter with enough impact
Expensive material to work with
Carbon composites in space
35% of all carbon fibre is used in the space industry. Here are just some of the projects and space-related uses of carbon fibre:
THE SPACE LAUNCH SYSTEM (SLS)
With its first launch having taken place on November 16th, the SLS will explore beyond Earth’s orbit. The launch vehicle’s core body is made from a mixture of carbon fibre and aluminium.
PARKER SOLAR PROBE
This craft studies the outermost part of the Sun’s atmosphere as well as solar winds. In order to withstand extreme temperatures, the probe is fitted with a sun shield made of carbon-fibre-reinforced carbon composites.
THE ORION MULTI-PURPOSE CREW VEHICLE
This NASA spacecraft is designed to take a crew of six beyond low Earth orbit all the way to the Moon, Mars, and other asteroids.
Carbon composites are used in several places across Orion’s design, such as its huge heat shield which is covered by a carbon fibre skin to provide extra protection from the extreme heat of Mars (around 2800℃).
Orion also features a Launch Abort System (LAS) which can carry the crew to safety in emergency situations. The LAS comprises three motors that work together to propel the craft. One of the motors contains a casing made of panels of carbon-fibre composite.
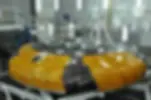
JAMES WEBB SPACE TELESCOPE (JWST)
To support the telescope’s mirrors and other instruments, the JSWT is fitted with a carbon fibre backplane. The telescope’s Mid Infra-Red Instrument (MIRI), a camera and spectrograph, which observes the red shifted light coming from distant galaxies and newly formed stars, also contains carbon-fibre-reinforced plastic.

ARTEMIS SUITS
Another use of carbon fibre within the space industry can be seen in spacesuits. In association with NASA and their 2025 Artemis lunar mission, Rhode Island’s School of Design headed a program called “Pack Your Bags! We’re Headed for the Moon” which led to a reinvention of the spacesuit. Unlike many other suits, this spacesuit contained carbon fibre. The suits were designed to protect astronauts from space dust, be comfortable, durable, and shield the crew from extreme weather.
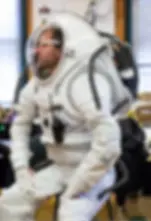
How does SIS make use of carbon fibre?
At Sent into Space, carbon fibre is an integral material we utilize for the construction of our spacecrafts. We use carbon composites for a number of reasons:
MATERIAL PROPERTIES OF CARBON FIBRE
Carbon fibre’s high strength-to-weight ratio means that when a spacecraft is designed to withstand the extreme forces experienced during a near space launch, the weight of the spacecraft can be minimised. Carbon composites, therefore, allow us to reach higher altitudes and reduce the cost of a launch due to their material properties.
OPTIMISING OUR MANUFACTURING TECHNIQUES WITH CARBON FIBRE
Here at Sent Into Space we design and build bespoke spacecraft in house. To do this, we use a multitude of manufacturing techniques from carbon fibre 3D printing, to milling, forming, forging and machining. Carbon composites are extremely versatile materials and in their various forms, we can ensure that our spacecraft are always pushing the limits of what is possible.
USING CARBON FIBRE TO INCREASE DIMENSIONAL STABILITY
Throughout their flight, our spacecraft are subject to a range of extreme temperature and pressure gradients. Carbon fibre is the perfect material to deal with these unique conditions. Carbon composites have dimensional stability, meaning their shape remains relatively constant throughout the duration of a space flight.